Sie überprüft Computerchips auf ihre Qualität, berechnet, wann eine Maschine gewartet werden muss oder kann „gute“ von „schlechten“ Teilen mühelos erkennen – Künstliche Intelligenz (KI) ist in weiten Bereichen der Industrie 4.0 Alltag. Die Bandbreite der Einsatzmöglichkeiten ist groß, wenngleich es einen Bereich gibt, in dem noch Arbeit geleistet werden muss: der Akzeptanz, dass Mensch und Maschine in der industriellen Fertigung von Gütern zusammenarbeiten können.
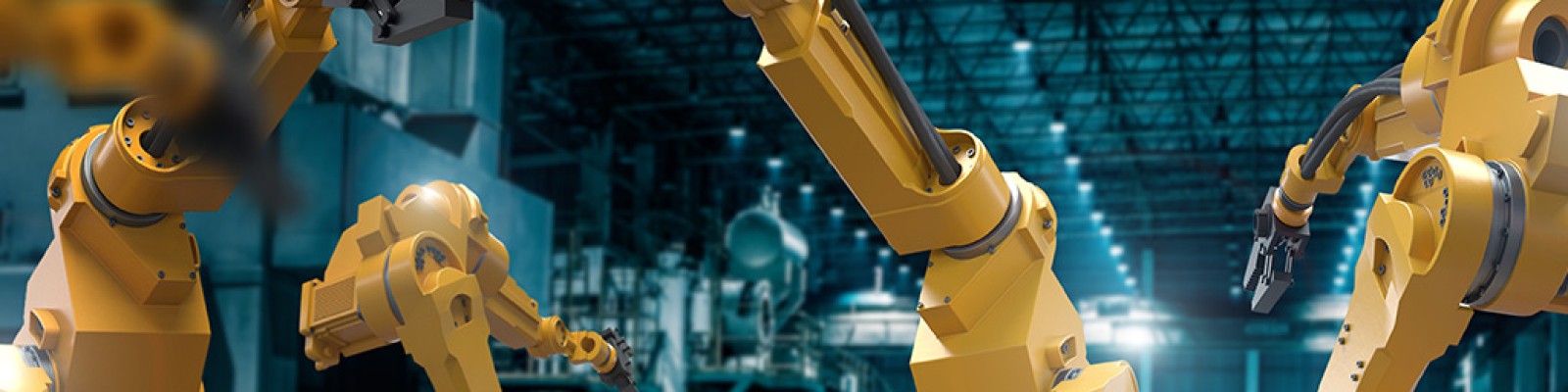
Text: Sandra Wobrazek
Von Big Data zu Right Data
Di 31. August 2021
Deep Learning
Beim Halbleiterhersteller Infineon Austria ist KI seit einigen Jahren ein relevantes Thema – in der Produktion selbst, aber auch, als Key-Enabler, indem KI basierte Produkte entwickelt und angeboten werden. Einsatzschwerpunkte sind Produktionsbereiche, in denen viele Daten zur Verfügung stehen, etwa in Qualitätssicherung, Fehleranalyse und Predictive Maintenance (vorausschauende Instandhaltung). „Dort wird versucht“, sagt Andreas Starzacher, Technical Lead for Data Science, Infineon Technologies Austria, „Prognosen herzustellen und das Gesamtsystem zu verbessern. KI sagt etwa vorher, dass zu einer bestimmten errechneten Wahrscheinlichkeit in zwei Tagen bei der Ionen-Implantation ein Bauteil ausfallen wird. So können im Vorfeld Wartungsarbeiten eingeplant werden. In der Fehleranalyse wiederum wird viel mit Deep Learning gearbeitet, um Fehler am Chip zu finden.“
Beim Halbleiterhersteller Infineon Austria ist KI seit einigen Jahren ein relevantes Thema – in der Produktion selbst, aber auch, als Key-Enabler, indem KI basierte Produkte entwickelt und angeboten werden. Einsatzschwerpunkte sind Produktionsbereiche, in denen viele Daten zur Verfügung stehen, etwa in Qualitätssicherung, Fehleranalyse und Predictive Maintenance (vorausschauende Instandhaltung). „Dort wird versucht“, sagt Andreas Starzacher, Technical Lead for Data Science, Infineon Technologies Austria, „Prognosen herzustellen und das Gesamtsystem zu verbessern. KI sagt etwa vorher, dass zu einer bestimmten errechneten Wahrscheinlichkeit in zwei Tagen bei der Ionen-Implantation ein Bauteil ausfallen wird. So können im Vorfeld Wartungsarbeiten eingeplant werden. In der Fehleranalyse wiederum wird viel mit Deep Learning gearbeitet, um Fehler am Chip zu finden.“
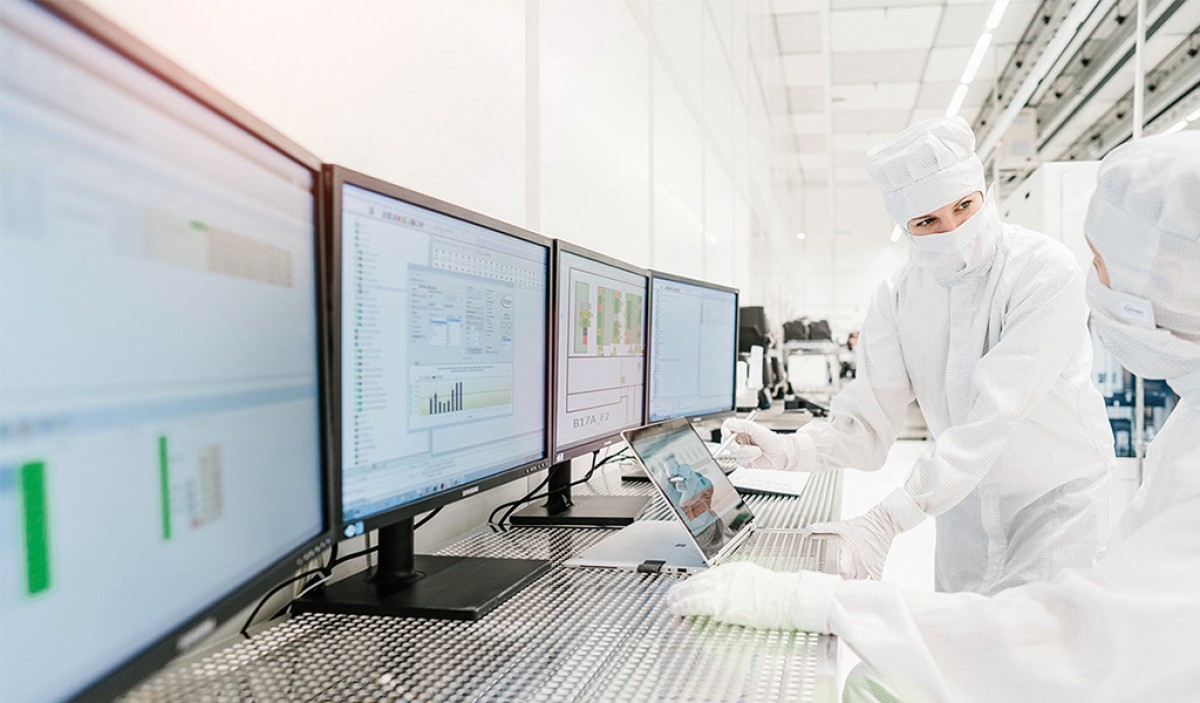
Im Reinraum von Infineon ist KI bereits Alltag
© Infineon Austria
Der Mensch wird in diesen Prozessen, so der Experte, weiterhin die wesentliche Rolle spielen – um im Notfall eingreifen und Fehler korrigieren zu können. Bei Infineon ist man davon überzeugt, dass es bei KI nicht um die Reduktion von Arbeitsplätzen geht, sondern um neue Chancen und neue Jobprofile. „Es gibt eine große Bandbreite an KI-Modellen, bei denen der Mensch als Supervisor gebraucht wird. Wir werden auch zukünftig Mitarbeiterinnen und Mitarbeiter benötigen, um das alles steuern zu können“, so Starzacher.
Eine der aktuellen Herausforderungen: die wachsende Fülle an Daten – Motto „von Big Data zu Right Data“ – richtig einzusetzen. Die Utopie, dass man Daten, ohne Vorverarbeitungsprozesse und Mitwirken von Expertinnen und Experten (expert judgement‘), einem neuronalen Netzwerk überlässt, wird, so der Infineon-Vertreter, nicht aufgehen. Das Unternehmen möchte zukünftig noch mehr Nutzen aus dem Einsatz digitaler Zwillinge (virtueller Systeme) ziehen. Aktuell nimmt Infineon im Rahmen des EU-Förderprogrammes Horizon 2020 unter anderem am DAPHNE Projekt teil, das sich der Frage widmet, wie Daten in der Industrie bestmöglich verarbeitet werden können. Andreas Starzacher: „Wir forcieren auch betriebliche Schulungen in KI, um IT-affinen Menschen den Einstieg ins Unternehmen leichter zu machen. Das gilt speziell für unsere neue Hochvolumensfabrik, wo zeitnah Leistungshalbleiter auf Basis von 300mm-Wafer (Anm. Siliziumscheiben) produziert werden sollen.“
Wiener Pilotfabrik
In der Wiener Seestadt wird erlebbar gemacht, zu was KI fähig ist – in einer Lern-, Innovations- und Demonstrationsfabrik, der TU Pilotfabrik Industrie 4.0. Im Bereich Innovation finden praxisnahe Forschungsprojekte mit der Industrie statt, während in der Lernfabrik Bachelor-, Master- und Doktorarbeiten durchgeführt werden. „Dabei werden kreative Wissenschaftlerinnen und Wissenschaftler mit Industrieunternehmen und deren Problemen konfrontiert. Für Firmen bieten wir Workshops in Robotik, 3D-Druck oder Mensch-Maschine-Kollaboration an“, so Claudia Schickling, Leiterin der Pilotfabrik.
Die dritte Säule der Ideenschmiede ist die Demonstrationsfabrik, deren Ziel Wissenstransfer ist. Im Rahmen von Führungen wird Industrie 4.0 der Öffentlichkeit zugänglich gemacht, inklusive der Herstellung eines 3D-Druckers, anhand dessen die Digitalisierung eines Produktionsprozesses verdeutlicht wird.
Einer der KI-Forschungsschwerpunkte: Machine Learning. Dabei werden Algorithmen verwendet, um Daten zu analysieren und digitale Zwillinge so zu trainieren, dass sie Voraussagen machen können, wie sich die Maschine verhalten wird. Seit März 2021 ist die Pilotfabrik Teil des bilateralen Projekts EuProGigant, das die Plattform GAIA-X nutzt, die eine sichere europäische Dateninfrastruktur schaffen soll. „Es geht“, sagt Claudia Schickling, „um Digitalisierung in der Produktion über verschiedene Standorte und um Vernetzung in Wertschöpfungsökosystemen. Datensouveränität ist ein großes Thema, denn viele Unternehmen stellen ihre Daten nicht gerne zur Verfügung, weil sie nicht wissen, was damit passiert. KI kann diese Datenmengen aber analysieren und Modelle feiner ausarbeiten.“ „Daten sind das neue Gold“ – dem kann die Pilotfabrik-Leiterin nur zustimmen. „Es entstehen viele Businessmodelle rund um Datenhandel. Denn durch Daten kann man Rückschlüsse ziehen und in vielen dieser Bereiche steckt KI dahinter – von Spracherkennung bis zum autonomen Fahren. Es geht darum, menschenzentrierte Fragen offen zu diskutieren, Datenschutz zu erhalten und aufzuklären, dass KI in einer immer komplexer werdenden Produktionswelt Arbeit abnimmt und den Menschen unterstützt.“
Eine der aktuellen Herausforderungen: die wachsende Fülle an Daten – Motto „von Big Data zu Right Data“ – richtig einzusetzen. Die Utopie, dass man Daten, ohne Vorverarbeitungsprozesse und Mitwirken von Expertinnen und Experten (expert judgement‘), einem neuronalen Netzwerk überlässt, wird, so der Infineon-Vertreter, nicht aufgehen. Das Unternehmen möchte zukünftig noch mehr Nutzen aus dem Einsatz digitaler Zwillinge (virtueller Systeme) ziehen. Aktuell nimmt Infineon im Rahmen des EU-Förderprogrammes Horizon 2020 unter anderem am DAPHNE Projekt teil, das sich der Frage widmet, wie Daten in der Industrie bestmöglich verarbeitet werden können. Andreas Starzacher: „Wir forcieren auch betriebliche Schulungen in KI, um IT-affinen Menschen den Einstieg ins Unternehmen leichter zu machen. Das gilt speziell für unsere neue Hochvolumensfabrik, wo zeitnah Leistungshalbleiter auf Basis von 300mm-Wafer (Anm. Siliziumscheiben) produziert werden sollen.“
Wiener Pilotfabrik
In der Wiener Seestadt wird erlebbar gemacht, zu was KI fähig ist – in einer Lern-, Innovations- und Demonstrationsfabrik, der TU Pilotfabrik Industrie 4.0. Im Bereich Innovation finden praxisnahe Forschungsprojekte mit der Industrie statt, während in der Lernfabrik Bachelor-, Master- und Doktorarbeiten durchgeführt werden. „Dabei werden kreative Wissenschaftlerinnen und Wissenschaftler mit Industrieunternehmen und deren Problemen konfrontiert. Für Firmen bieten wir Workshops in Robotik, 3D-Druck oder Mensch-Maschine-Kollaboration an“, so Claudia Schickling, Leiterin der Pilotfabrik.
Die dritte Säule der Ideenschmiede ist die Demonstrationsfabrik, deren Ziel Wissenstransfer ist. Im Rahmen von Führungen wird Industrie 4.0 der Öffentlichkeit zugänglich gemacht, inklusive der Herstellung eines 3D-Druckers, anhand dessen die Digitalisierung eines Produktionsprozesses verdeutlicht wird.
Einer der KI-Forschungsschwerpunkte: Machine Learning. Dabei werden Algorithmen verwendet, um Daten zu analysieren und digitale Zwillinge so zu trainieren, dass sie Voraussagen machen können, wie sich die Maschine verhalten wird. Seit März 2021 ist die Pilotfabrik Teil des bilateralen Projekts EuProGigant, das die Plattform GAIA-X nutzt, die eine sichere europäische Dateninfrastruktur schaffen soll. „Es geht“, sagt Claudia Schickling, „um Digitalisierung in der Produktion über verschiedene Standorte und um Vernetzung in Wertschöpfungsökosystemen. Datensouveränität ist ein großes Thema, denn viele Unternehmen stellen ihre Daten nicht gerne zur Verfügung, weil sie nicht wissen, was damit passiert. KI kann diese Datenmengen aber analysieren und Modelle feiner ausarbeiten.“ „Daten sind das neue Gold“ – dem kann die Pilotfabrik-Leiterin nur zustimmen. „Es entstehen viele Businessmodelle rund um Datenhandel. Denn durch Daten kann man Rückschlüsse ziehen und in vielen dieser Bereiche steckt KI dahinter – von Spracherkennung bis zum autonomen Fahren. Es geht darum, menschenzentrierte Fragen offen zu diskutieren, Datenschutz zu erhalten und aufzuklären, dass KI in einer immer komplexer werdenden Produktionswelt Arbeit abnimmt und den Menschen unterstützt.“
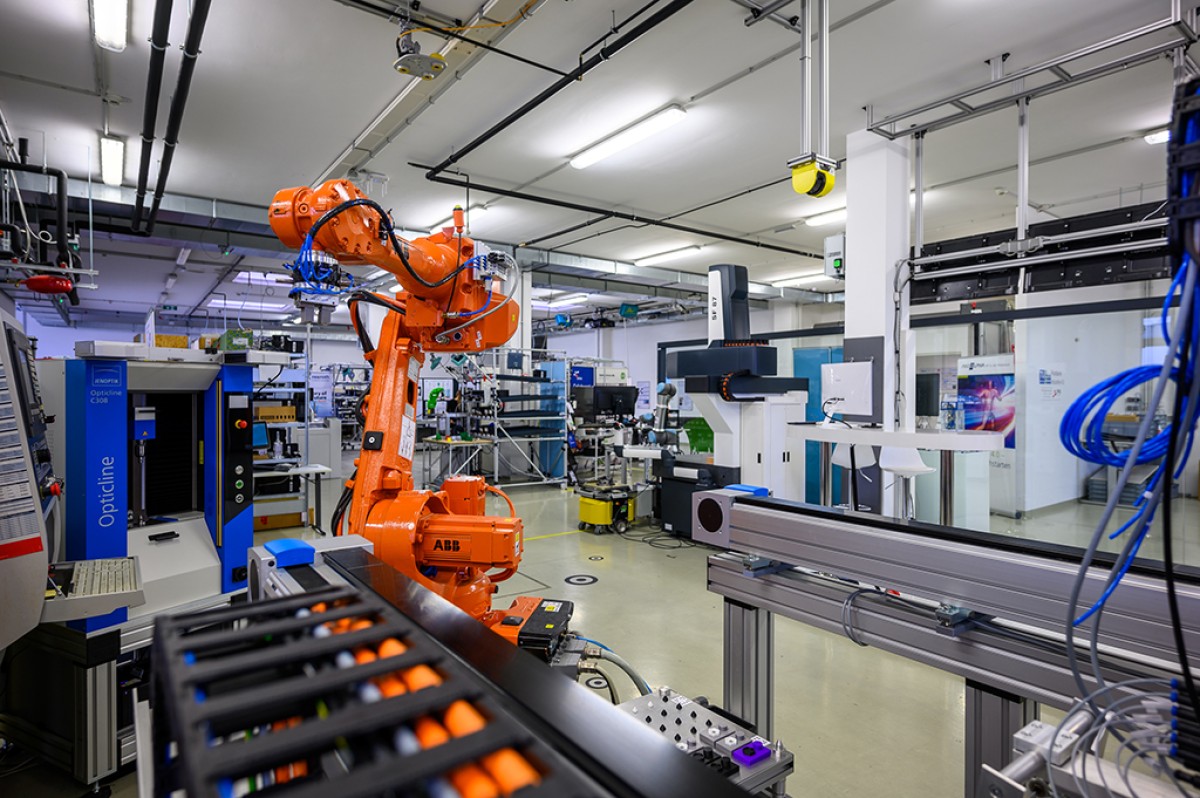
In der Wiener Pilotfabrik wird Industrie 4.0 erlebbar gemacht
© Matthias Heisler
Teil des Wertschöpfungsprozesses
Auch bei Siemens setzt man auf KI. Im Siemens Elektronikwerk Amberg (EWA) ist Industrie 4.0 bereits Realität, gilt der Standort doch als digitale Leuchtturmfabrik, die vom Weltwirtschaftsforum (WEF) in dessen Global Lighthouse Network aufgenommen wurde. Hier werden auch Elektronikboards für Steuerungen produziert. Am Ende der Produktion untersucht ein Röntgengerät, ob die Lötpunkte auf den Boards korrekt angebracht sind, wie Lukas Gerhold, bei Siemens Österreich zuständig für Digitalisierung im Bereich Digital Industries, sagt. Um die Produktionsmenge zu erhöhen, hätte ein weiteres der 500.000 Euro teuren Geräte angeschafft werden müssen – ein Fall für KI. „Aufgrund der bestehenden Produktion“, sagt Gerhold, „hat man alle relevanten Informationen, um zu wissen, wann es ein ,good Board‘ und wann ein ,schlecht Board‘ ist. Mit diesen Informationen wurde ein KI-Modell erstellt, das errechnet, welche Qualität das produzierte Board hat – und nur noch die ,schlecht Boards‘ in die X-Ray schickt.“ Das Ergebnis: um 30 Prozent reduzierte Röntgentests und der Verzicht auf die Anschaffung eines zweiten Röntgengerätes bei gleichbleibender Qualität.
Auch bei Siemens setzt man auf KI. Im Siemens Elektronikwerk Amberg (EWA) ist Industrie 4.0 bereits Realität, gilt der Standort doch als digitale Leuchtturmfabrik, die vom Weltwirtschaftsforum (WEF) in dessen Global Lighthouse Network aufgenommen wurde. Hier werden auch Elektronikboards für Steuerungen produziert. Am Ende der Produktion untersucht ein Röntgengerät, ob die Lötpunkte auf den Boards korrekt angebracht sind, wie Lukas Gerhold, bei Siemens Österreich zuständig für Digitalisierung im Bereich Digital Industries, sagt. Um die Produktionsmenge zu erhöhen, hätte ein weiteres der 500.000 Euro teuren Geräte angeschafft werden müssen – ein Fall für KI. „Aufgrund der bestehenden Produktion“, sagt Gerhold, „hat man alle relevanten Informationen, um zu wissen, wann es ein ,good Board‘ und wann ein ,schlecht Board‘ ist. Mit diesen Informationen wurde ein KI-Modell erstellt, das errechnet, welche Qualität das produzierte Board hat – und nur noch die ,schlecht Boards‘ in die X-Ray schickt.“ Das Ergebnis: um 30 Prozent reduzierte Röntgentests und der Verzicht auf die Anschaffung eines zweiten Röntgengerätes bei gleichbleibender Qualität.
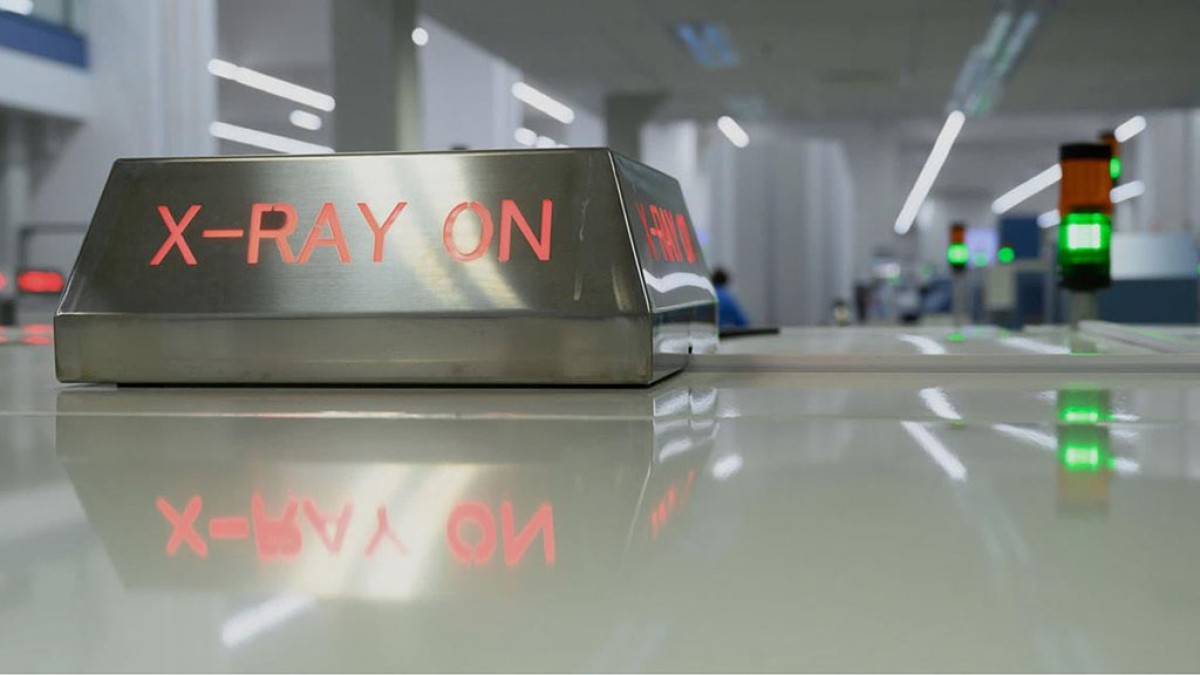
Bei Siemens ersetzt KI ein teures Röntgen-Kontrollgerät
© Siemens
Genau jener Bereich der Value Chain, der Wertschöpfungskette, ist es, in dem Siemens KI zukünftig verstärkt in Maschinen platziert sehen möchte. „Zukünftig werden vor allem komplexe Applikationen von KI übernommen. Dort, wo es keine numerischen Korrelationen gibt, und Kreativität gefragt ist, wird weiterhin der Mensch gebraucht.“ Wo sind die Grenzen von KI in der Industrie? Siemens zum Beispiel möchte seinen Kunden verstärkt die Welt der KI und der Datenverarbeitung näherbringen, stößt aber noch auf den Gap zwischen Information Technology (IT) und Operational Technology (OT). Während in der IT Algorithmen und Cloud-Anbindung Alltag sind, basiert die OT-Welt auf elektrischen Systemen. „Um auch dort KI einführen zu können“, weiß KI-Experte Gerhold, „brauchen wir einfache Mittel, um die Produktionsprogrammierer an die KI-Welt heranzuführen.“ Das Ziel: dass Nutzer aus ihren Maschinen leicht Daten gewinnen und lernen, wie sie sie im Rahmen von Data Analytics nutzen. Aus Daten KI-Modelle zu erstellen und die wieder in die Produktion zu bringen, ist dank verschiedenster bereits existierender Tools, so Lukas Gerhold, der letzte „und zugleich einfachste Schritt.“
Sandra Wobrazek ist Autorin und freie Redakteurin.
Sandra Wobrazek ist Autorin und freie Redakteurin.